Lean of QRM? Wij vroegen het Packo Inox. Het metaalbewerkingsbedrijf uit Diksmuide produceert industriële pompen en hygiënische componenten voor de voedingsindustrie. In hun drive om continu te verbeteren ontwikkelde het bedrijf een eigen variant op Lean en nam het de eerste stappen in QRM met behulp van het shop floor control systeem van PROPOS. Is het bedrijf nu helemaal overgestapt op QRM? ‘Nee’, zo legt Managing Director Danny Maenhout uit: ‘Waarom kiezen? Het gaat uiteindelijk om meer flow: neem het beste van beiden.’
Wilt u dit artikel in PDF lezen of downloaden? Bekijk het hier!
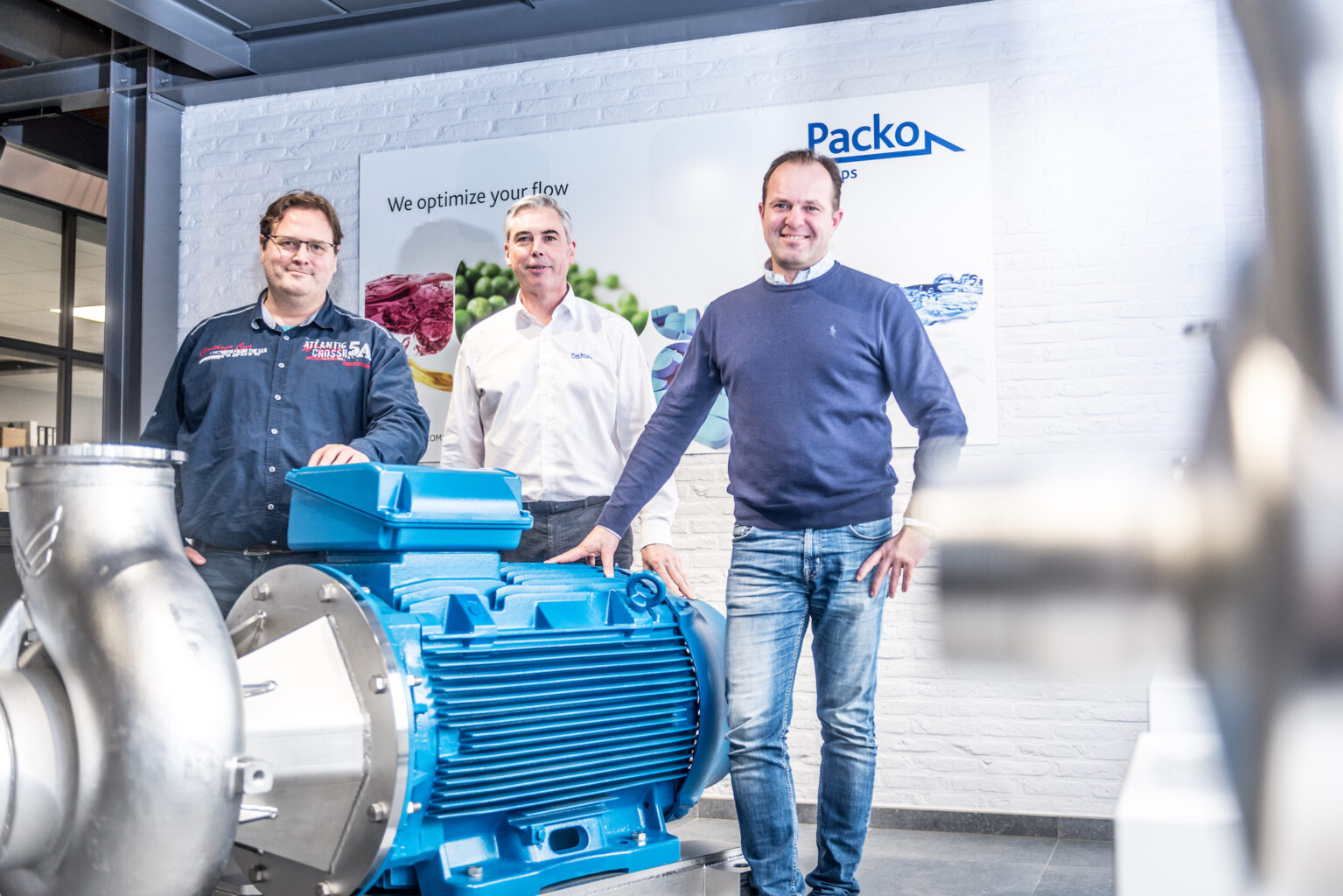
“Wordt het Lean of QRM? Waarschijnlijk een eigen invulling. Neem het beste van beiden.”
In de moderne fabriek van Packo Inox vallen direct een aantal zaken op. Er is rust op de vloer. Boxen en materialen staan opgeruimd en op nummer geordend te wachten op de volgende order die in bewerking genomen kan worden. Het gereedschap hangt er symmetrisch geordend bij. Het bedrijf heeft drie afdelingen waar verschillende bewerkingen uitgevoerd worden, van manueel lassen tot robotlassers, van ontwerp tot assemblage en nabewerking. De stappenproductie van de afdelingen Industriële Pompen, Hygiënische Componenten en Oppervlaktebehandeling RVS kennen echter belangrijke verschillen.
Van Lean naar flow
Zoals veel productiebedrijven worstelde Packo Inox tot voor kort met haar doorlooptijden, de onvoorspelbaarheid in het proces, onduidelijke orderstatussen en het continu brandjes blussen op de vloer. Hierdoor kwamen de assemblage en levering onder druk te staan. ‘In 2004 zijn we begonnen met Lean’, legt Maenhout uit. ‘Dit werkte goed voor de industriële pompen die een grotendeels gestandaardiseerd proces hebben. We zijn echter vrij snel afgestapt van de naam ‘Lean’ omdat we er onze eigen invulling aangeven. We hebben gezocht naar de optimale flow in het bedrijf. Is dat Lean of is dat QRM? Waarschijnlijk een Packo-invulling van beiden. Voor het ene productiedeel is Lean geschikt, voor een ander QRM. We kunnen van beide principes leren.’
High-mix low-volume
Packo Inox ontwikkelde een eigen Lean variant, Creating Flow, met takttijden en standaardroutings. Zo slaagde het erin om de werkdruk te spreiden, de flow visueler te maken en doorlooptijden voor de afdeling pompen te halveren. Hoewel het systeem veel succes opleverde voor de meer gestandaardiseerde productie van pompen, liep Packo Inox bij de afdeling Hygienic Components toch nog tegen problemen aan. Lean bleek minder toereikend voor de high-mix low-volume productie. Maenhout legt het probleem uit: ‘Bij Hygienic Components hebben we niet alleen te maken met zeer veel onderdelen stukken, maar per stuk ook nog eens met veel verschillende flows. We hebben ook heel veel stukken in pompen, maar of het een kleine of een grote pomp is, je hebt altijd wel ongeveer een gelijk aantal onderdelen en een gelijke flow. Bij hygienic components echter hebben we zo’n 1700 verschillende eindartikelen die in de productie die elkaar soms kruisen in de productie, soms niet, en dan weer samenkomen.’
“Lean bleek minder geschikt voor de high-mix low-volume productie”
Naast de uitdagingen van de high-mix low-volume productie werd het bedrijf geconfronteerd met een andere: na jarenlange trouwe dienst ging de productiemanager met pensioen. Maenhout: ‘Dit was de man die alles wist van de hygienic components, die heeft alles meegemaakt. Van de opstart met een paar man tot het middelgrote bedrijf wat het nu is, met 130 medewerkers. Hij had dus alle kennis van de productiestappen in zijn hoofd. Maar om al die kennis over te zetten naar een organisatie, dat kun je niet één op één doen. Plus, je hebt te maken met de borging van je kennis. Met de komst van onze nieuwe productieleider Stefaan gingen wij op zoek naar een ondersteunende software die die flows heel zichtbaar zou kunnen maken.’
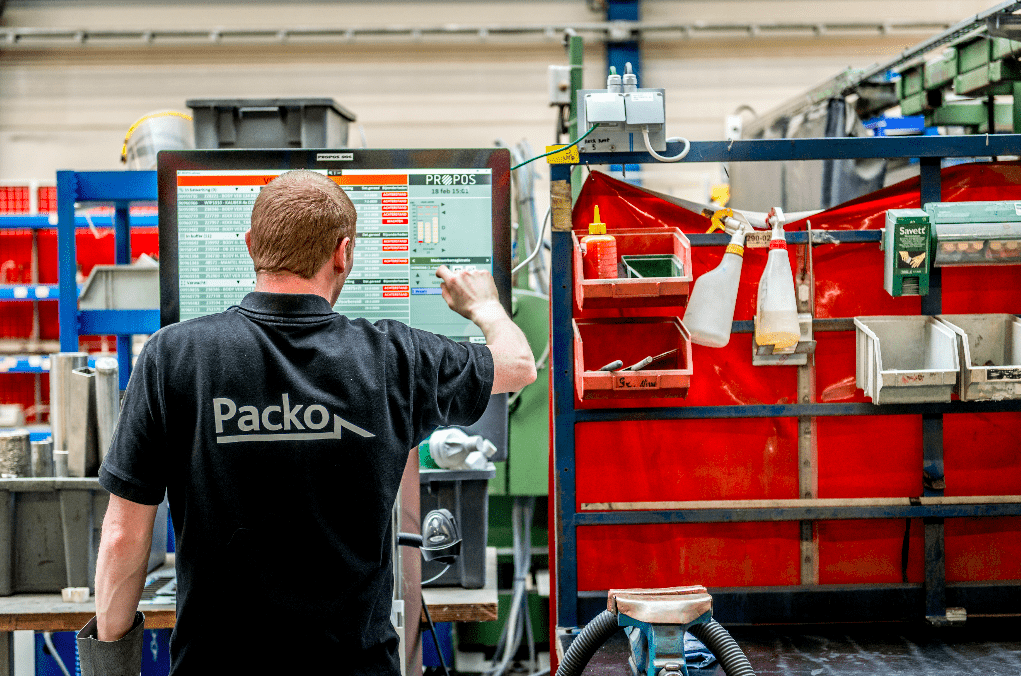
QRM én shop floor control
Maenhout ging op zoek naar een manier om ook het productieproces van de high-mix low-volume afdeling van hygienic components te optimaliseren: ’Wij zijn aangesloten bij Lean Lead. Dit netwerk specialiseert zich in het samenbrengen van bedrijven rond verschillende onderwerpen. Het betreft vooral middelgrote bedrijven. Via onze Lean contacten kwamen wij er achter dat QRM voor wat wij deden meer geschikt zou zijn. Zo leerden wij via andere bedrijven over het shop floor control systeem van PROPOS. Van meerdere kanten zagen wij de positieve resultaten van PROPOS. Zo ben ik langsgegaan bij QRM pioniers Provan en BOSCH Scharnieren.
Met de komst van PROPOS, dat op Lean én QRM-principes gebaseerd is, werd Quick Response Manufacturing eigenlijk als vanzelf ingevoerd: ‘Wij geloven heel erg in QRM. We zijn ook geslaagd voor de QRM Silver Opleiding. Wij willen QRM daarom ook stap voor stap invoeren. Eerst willen we meer inzichten krijgen. We hebben er daarom bewust voor gekozen om met PROPOS te starten, zodat we de flow zichtbaar kunnen maken, voordat we ingrijpende QRM stappen gaan doorvoeren. Het voordeel van PROPOS is bovendien dat de principes van QRM in de software zijn ingebouwd. Je hoeft niet veel extra toe te passen. Dat vergemakkelijkte het proces.’
QRM: meer op competenties
De stap naar QRM zorgde voor een ommezwaai in de manier van werken voor veel medewerkers. Bovendien moest de werkvloer anders ingericht worden, door bepaalde bewerkingen en machines te groeperen in werkcellen, zo legt de nieuwe productiemanager Stefaan Vanhauter uit: ‘Na de live-gang zijn we aan de competenties van onze medewerkers gaan werken. Die zaten nog een beetje in hun comfortzone. Dat vroeg een mentaliteitsverandering. Nu moet je de order met de meeste prioriteit nemen en niet jouw favoriet. Ik heb een gedetailleerde competentiematrix opgesteld en celindeling gemaakt voor PROPOS live ging. Op basis daarvan hebben we per cel bepaald: wat kunnen onze medewerkers en welke vaardigheden moeten ze nog leren?’
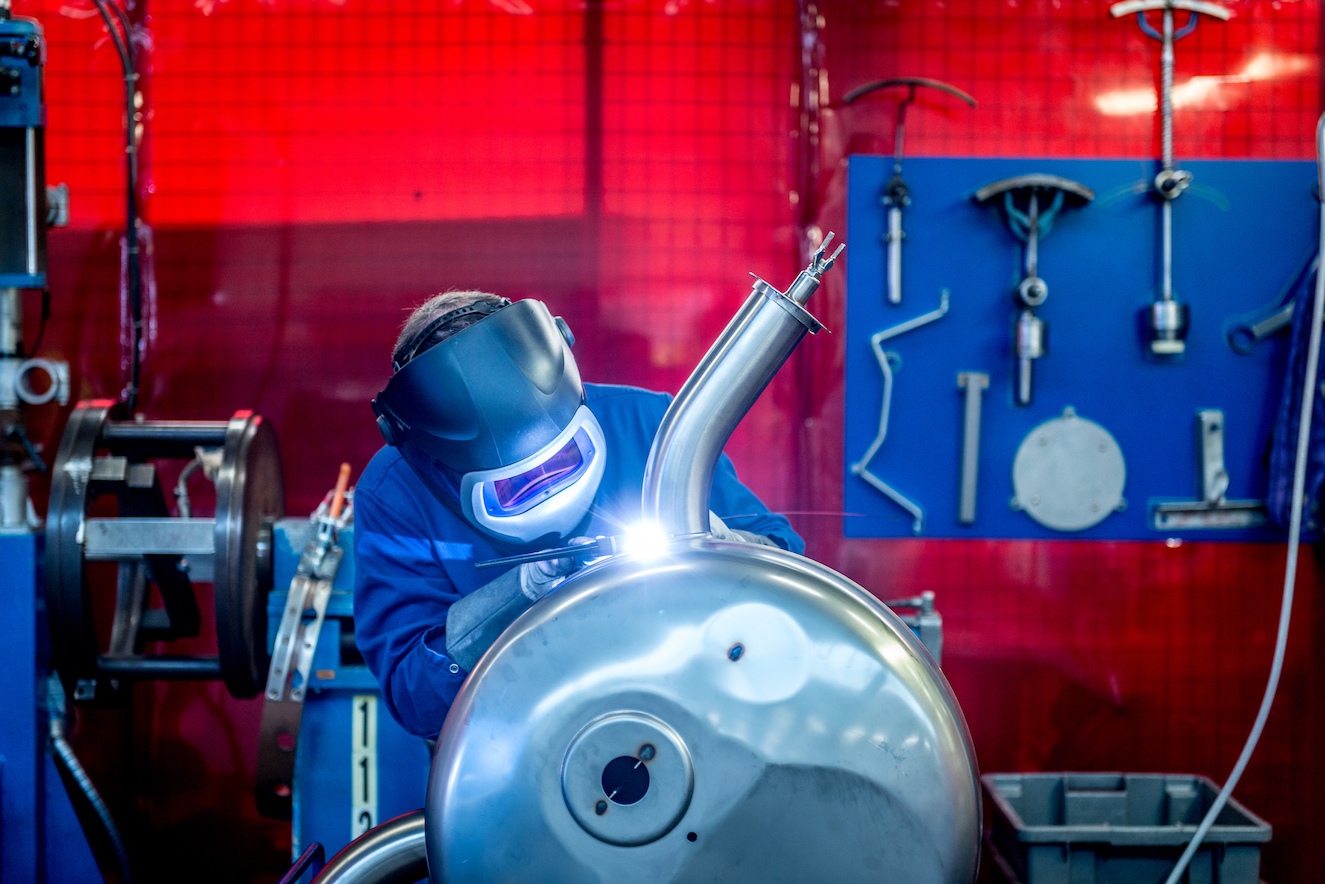
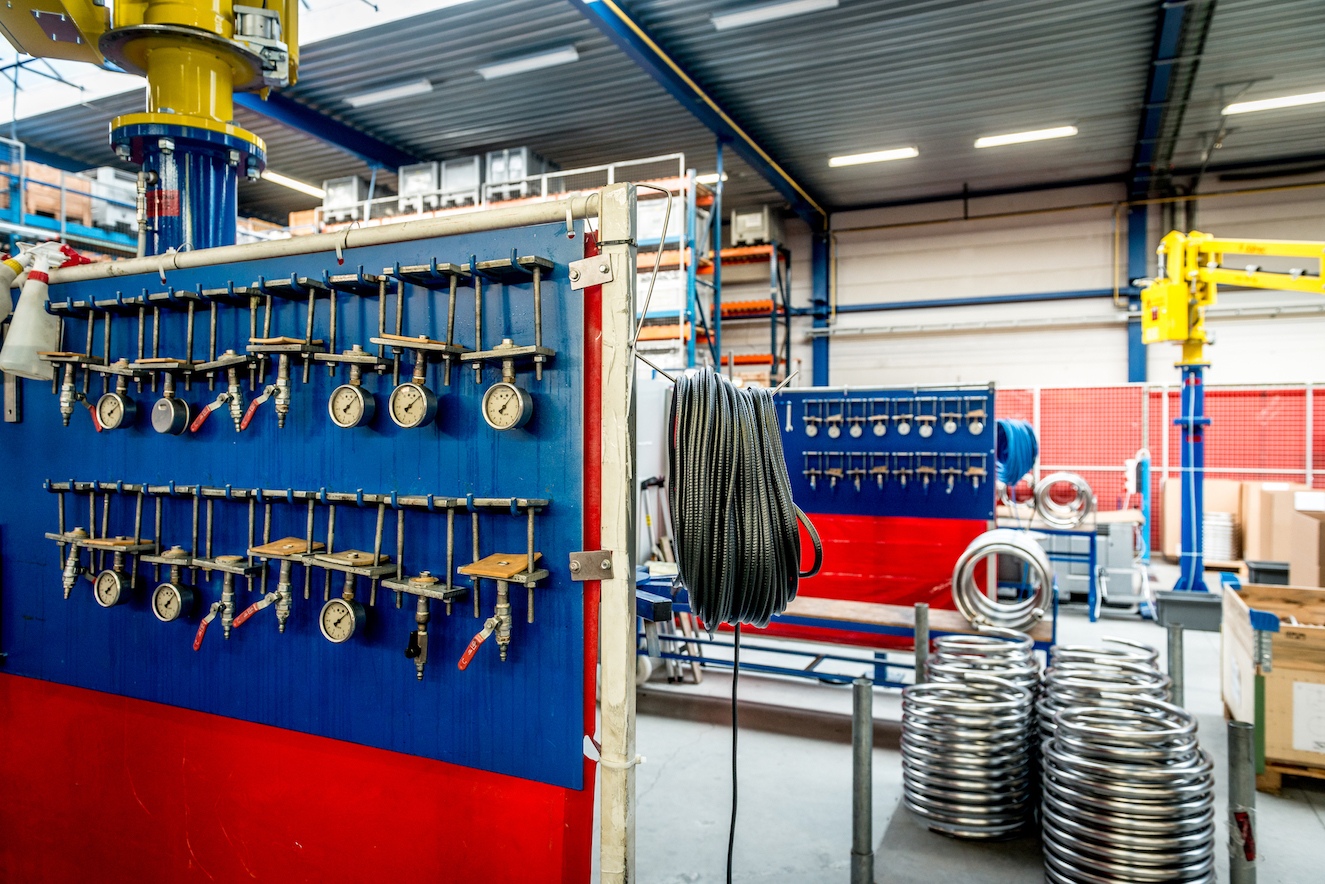
Vanhauter: ‘Om de veranderde manier van werken tot een succes te maken, hield ik het behapbaar. We geven enkel door wat er nu moet gebeuren en niet alle orders in één keer. Zo minimaliseer je dat mensen aan de verkeerde order werken. Ook gaf het medewerkers een gevoel van overzicht. Er lag niet nog een hele stapel te wachten.’
“QRM zorgde voor een ommezwaai in de werkwijze. We zijn meer op competententies gaan zitten. Wat kunnen medewerkers, wat moeten ze nog leren?”
QRM zorgde ook voor een mindsetverandering
‘De mensen konden echter nog niet echt vatten hoe de werkwijze was veranderd’, vervolgt Vanhauter. “Dit product heb ik maandag al gemaakt, waarom op vrijdag weer? Waar zijn jullie mee bezig?” Toen hebben we laten zien hoe je eigenlijk sneller door kan wanneer je alleen op behoefte draait en niet op stock die je eigenlijk niet nodig hebt. Dat zorgde voor inzicht en begrip; hadden we dat niet gedaan, dan hadden ze misschien frustratie gehouden door het onbegrip over de werkwijze. En die gedachtengang, is nu volledig weg. Ze vinden de werkwijze nu vanzelfsprekend.’
Maenhout sluit hier op aan: ‘We hebben heel weinig insteltijden binnen de afdeling Hygienic Components. Daarom is maken wat je nodig hebt zonder extra’s de perfecte filosofie. Voor de mensen is het een mindsetverandering. Op die manier werken sluit goed aan bij een goed georganiseerd geheel.’
Met de inzichten uit de data analyses van PROPOS en de eerste resultaten met QRM werd Maenhout al snel duidelijk waar de grootste winst van het bedrijf lag: ‘Wat betreft de flow hebben we geleerd dat de echte touchtijd minimaal is, elke handeling is maar een paar minuten werk. Dus dan is de winst om die leverbetrouwbaarheid en de levertijd in te korten. Dat doe je door alles buiten de touchtijd, de whitespace, zo goed mogelijk te organiseren. De touchtijd staat niet ter discussie, maar daar zitten nog zóveel stappen tussen.’
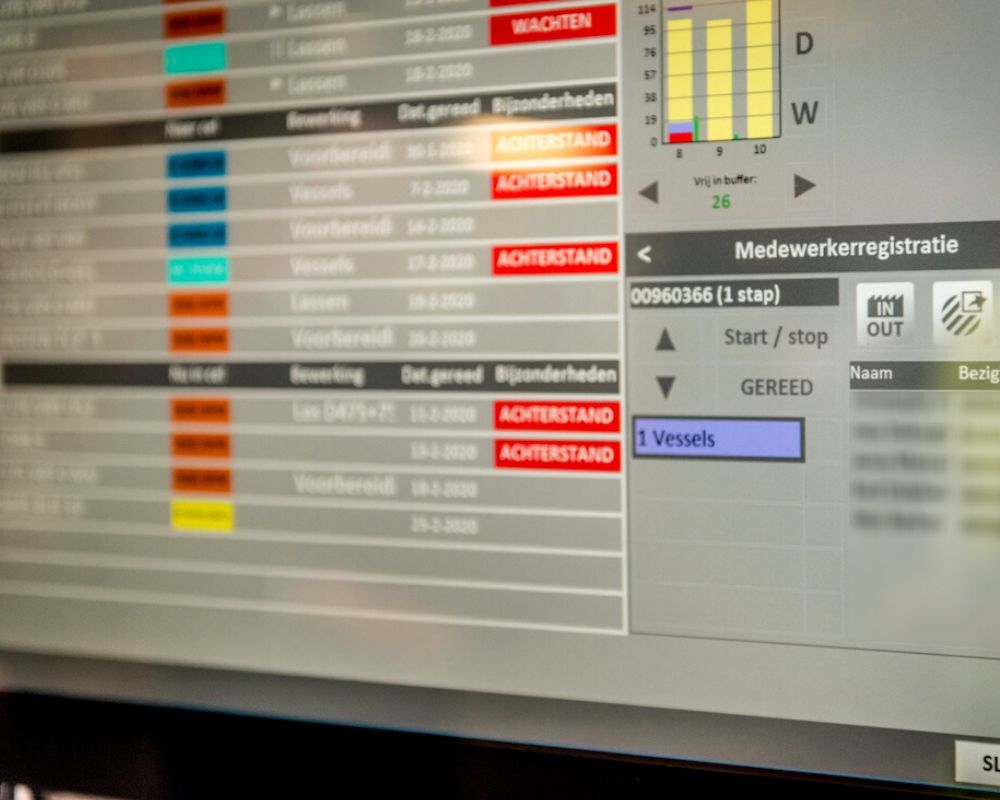
Quick wins als basis van verandermanagement
Op het moment werkt Packo Inox met 19 productiecellen. Dat is vrij veel, maar die keuze is bewust gemaakt. Maenhout: ‘We hebben nu teveel werkcellen. Dat willen we in stappen verminderen. Je spreekt over verandering, dus deze aanpak was al een hele stap voor de mensen. Al ging de overgang wel erg soepel met de PROPOS-schermen. Dat gebruiksgemak had voor de mensen direct meerwaarde. Ook de taken van de medewerkers veranderden: binnen de werkcel niet meer enkel een taak doen, maar 80% van de taken doen. Aangezien dit een automatisch gevolg is van de implementatie van PROPOS hebben we gezegd: we beginnen eerst hiermee. Je moet dergelijke grote veranderingen rustig doorvoeren.
Op den duur kunnen we, en zullen we, ervoor kiezen om nog iets meer te gaan inkrimpen, maar dat betekent ook meer opleiding en belangrijke layout-wijzigingen. Dat zijn vrij grote stappen die je naar de mensen toe moet nemen. Vandaar dat we het stap voor stap doen. Op dit moment ligt de focus op quick wins. De resultaten kwamen gelukkig snel en deze gebruiken we om uit te leggen waarom we nog meer cellen gaan groeperen en waarom we nog meer activiteiten in een cel gaan uitvoeren. Zo kan je laten zien: dit is waar we naartoe willen.’
“Wij voeren veranderingen stap voor stap in, met de focus op quick wins. Zo kunnen de mensen wennen.”
Lean of QRM? Dat leer je door te doen
En die richting, is dat Lean of QRM? ‘Dat is afhankelijk van de behoefte’, stelt Vanhauter. ‘We hebben verschillende delen van het productieproces ook verschillend ingericht. Lean is meer geschikt voor repetitief werk, QRM bij meer variatie.’ Nog geen kleuren en lijnen bij de werkcellen dus. ‘Die indeling gaat ook een beetje met trial en error. Soms ga je van Lean naar QRM principes en soms juist andersom. PROPOS heeft de discussie geopend van hetgeen dat we leren, zien en voelen op de vloer: hoe kunnen we het anders doen? Kunnen we die activiteit anders doen, elders uitvoeren? Je leert uit de dingen waar je mee bezig bent. We zijn bewust breed begonnen. We hebben veel cellen gecreëerd, en van daaruit kan je weer meer stappen zetten in de QRM aanpak. We hebben al wel gezien aan de routings van de artikelen dat we bepaalde activiteiten beter kunnen fuseren. Al doende leert men.’
Een voorbeeld van die keuze om principes te kiezen op basis van behoefte is bij robotlassen. Vanhauter: ‘De afdeling Robotlassen is de enige afdeling waar we nog met een vorm van voorraad werken. Dat komt omdat we hier veel ombouwtijd nodig hebben. Bij andere afdelingen geldt dat niet. Daar is het ‘als we geen verkooporder hebben, gaan we het ook niet produceren’. Daarom werken we niet per se met Lean of QRM, maar een eigen variant. Toegespitst per afdeling. Dit zijn dure machines met veel ombouwtijd, die kan je niet voor een enkel stuk laten draaien, dat is te gek voor woorden. Wel wetende dat je een groot volume nodig hebt op jaarbasis, natuurlijk. Tien tot twintig stuks worden gewoon door de manuele lassers gedaan. Bij de robots spreken we echt van volumes van meer dan duizend per jaar. Zo overwegen we continu, wat doen we wel en wat doen we niet?’
Succes met optimal flow en shop floor control
‘De evolutie die we hebben meegemaakt is ongekend’, vertel Maenhout trots. ‘Onze WIP voor hygienic components is meer dan gehalveerd. In het begin hebben we bij de lasafdeling rekken moeten bijzetten. Daar hadden we enorm veel materiaal op de werkvloer. Nu is dat weg en hebben we eigenlijk teveel rekken staan. Toendertijd werkten we veel met achterstanden, dat was toen ook normaal door de manier van werken. Nu hebben we dat helemaal weggewerkt. Als ik nu bij hygienic components door de fabriek loop, zie ik op de schermen in één oogopslag hoe het ervoor staat.’
“De WIP is gehalveerd, de leverbetrouwbaarheid gestegen en we hebben een van onze beste jaren gehad qua omzet.”
De leverbetrouwbaarheid op de afdeling Hygienic Components is dankzij de inzet van QRM en PROPOS gestegen van 50 procent tot 80 en soms zelfs 90 procent. Dat dit percentage niet hoger ligt is niet eens te wijten aan de eigen inrichting, maar aan externe factoren, zo legt Maenhout uit. ‘Dat resterende percentage ligt meer aan de kant van externe leveranciers, bijvoorbeeld als wij de stukken die we nog nodig hebben niet op tijd geleverd hebben gekregen.’ Hoewel de gestegen leverbetrouwbaarheid geen doelstelling op zich was, geeft het wel een duidelijke optimalisatie van de productieflow aan. ‘De afdeling Hygienic Components is in die zin specifiek dat klanten orders hebben met veel onderdelen, en die moeten allemaal op hetzelfde moment klaar zijn. Vroeger was maar de helft van de orders tegelijk gereed. Dan stonden er een aantal dingen veel te vroeg klaar, of veel te laat, of moest de zending wachten op één of twee stukjes. Nu kijken we, hoe kunnen we het zo snel mogelijk versturen? En niet op één dag maar over heel de week verspreid. Zo haal je een heleboel druk weg. We zien bijvoorbeeld in de bezetting van het magazijn dat we nu meer components versturen maar 1 FTE minder hebben omdat het werk beter verdeeld is.’
Toekomstmuziek
Het meest opmerkelijke verschil? Maenhout: ‘We hebben vorig jaar in hygienic components één van onze beste jaren gehad in omzet, maar het is heel rustig door productie gegaan. Dat is opmerkelijk. Je kunt dat niet vertalen in exacte cijfers, maar dat is gewoon een gevoel dat je dagelijks hebt.’
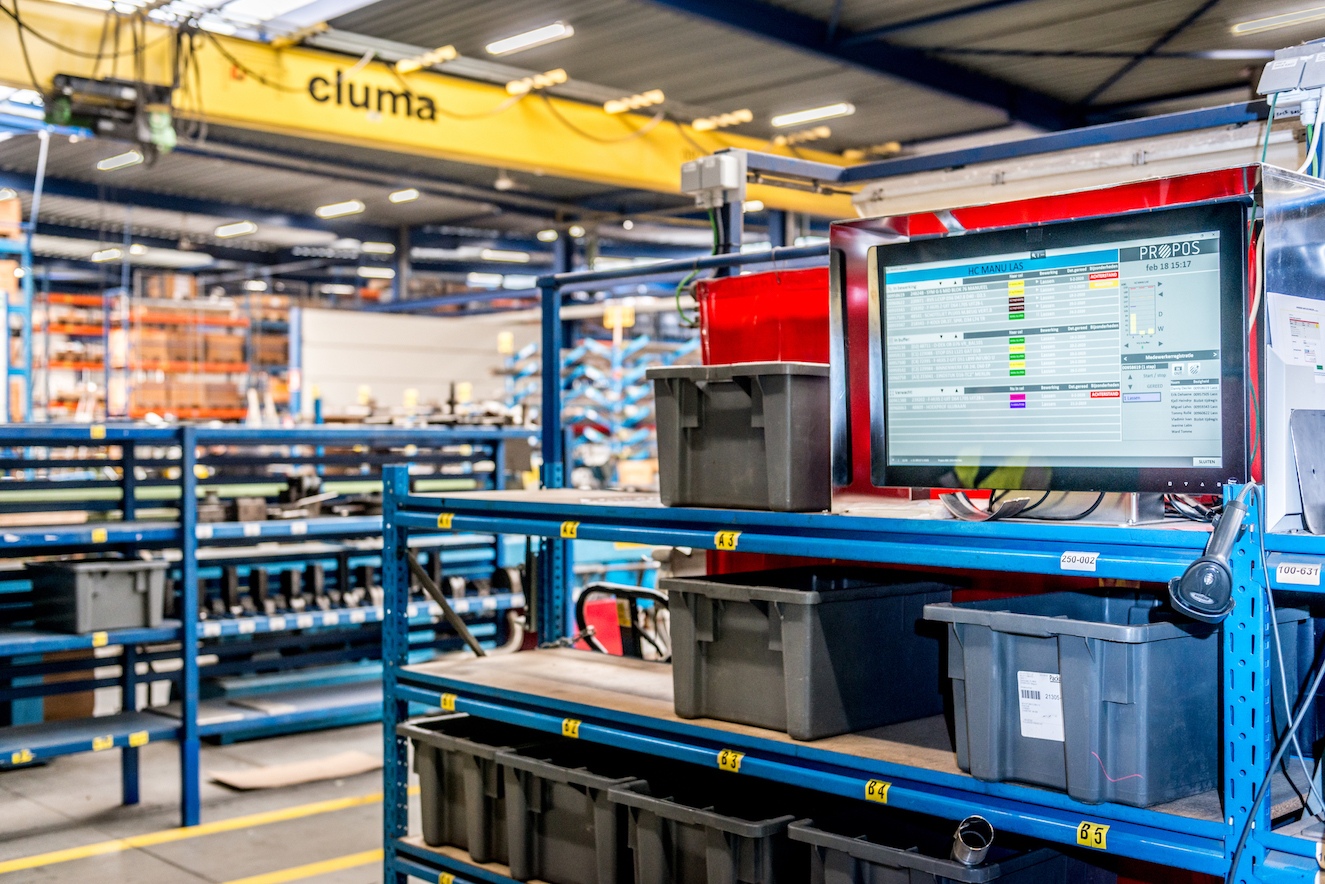
‘Op de langere termijn willen we daarom QRM verder gaan uitwerken. De bedoeling is om PROPOS zoveel mogelijk in de hele fabriek in te zetten, waar het zich het beste toe leent, uiteraard. Dat zorgt niet alleen voor uniformiteit, maar ook voor flexibiliteit. Zodat je in de toekomst bijvoorbeeld de planner van industriële pompen in zou kunnen zetten bij hygiënische componenten, en vice versa. Daarnaast zorgen we met de mogelijkheden van PROPOS ook voor een stukje kwaliteit- en visueel management. We hebben PROPOS in de praktijk gezien, samen met de toepassing van QRM, bij BOSCH Scharnieren. Daar gaat men zelfs nog een stap verder. Als er geen werk meer is in een bepaalde cel halen zij gewoon die medewerkers naar een andere cel. De medewerkers daar zijn volledig gecrosstrained. Dat is voor ons nog toekomstmuziek.’
Lees meer over hoe Packo Inox PROPOS inzet als tool voor visueel management en kwaliteitsmanagement
Of bekijk de volledige case in PDF: ‘Packo Inox borgt kennis én kwaliteit met PROPOS.’
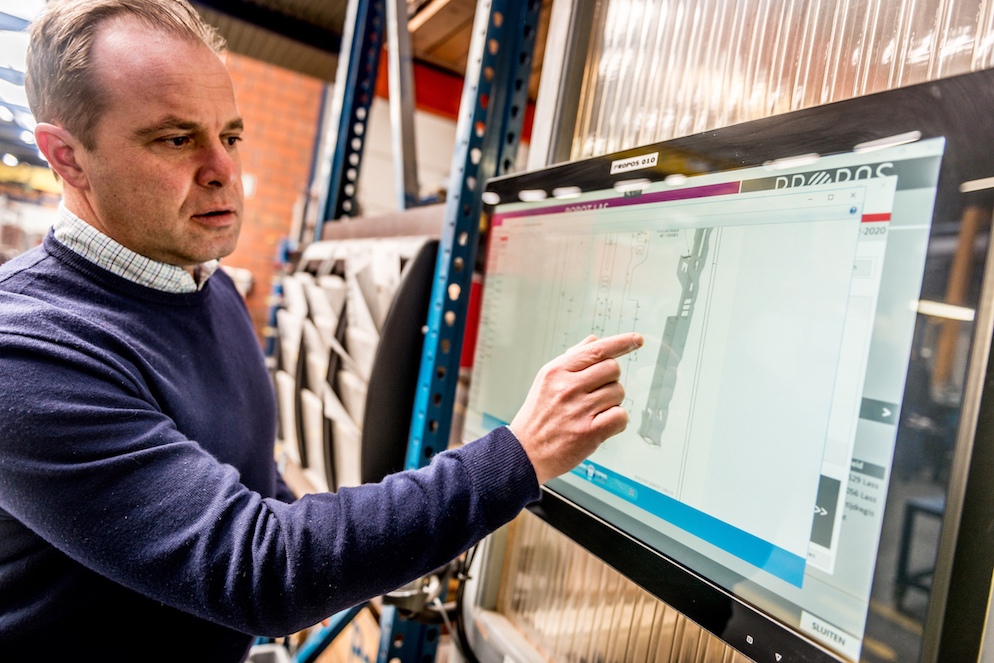
8 redenen waarom Packo voor PROPOS shop floor control kiest
- Ondersteuning met high-mix low-volume
- Bewezen in de praktijk
- Eenvoudig en intuïtief
- Uitstekende ROI
- Geschikt voor MS Dynamics 365
- Dynamische aanvulling op ERP
- Borgen van kennis en kwaliteit
- Visueel management
PROPOS koppeling met het ERP systeem MS Dynamics
Omdat PROPOS verschillende koppelingen beschikbaar heeft, kan PROPOS vaak binnen 3 tot 4 maanden geimplenteerd worden. Zo had PROPOS al een koppeling beschikbaar voor het ERP systeem MS Dynamics.
Belangrijk onderdeel van de keuze van Packo Inox voor PROPOS was bijvoorbeeld ook de mogelijkheid om over te kunnen stappen naar het nieuwe MS Dynamics systeem, Microsoft Dynamics 365.
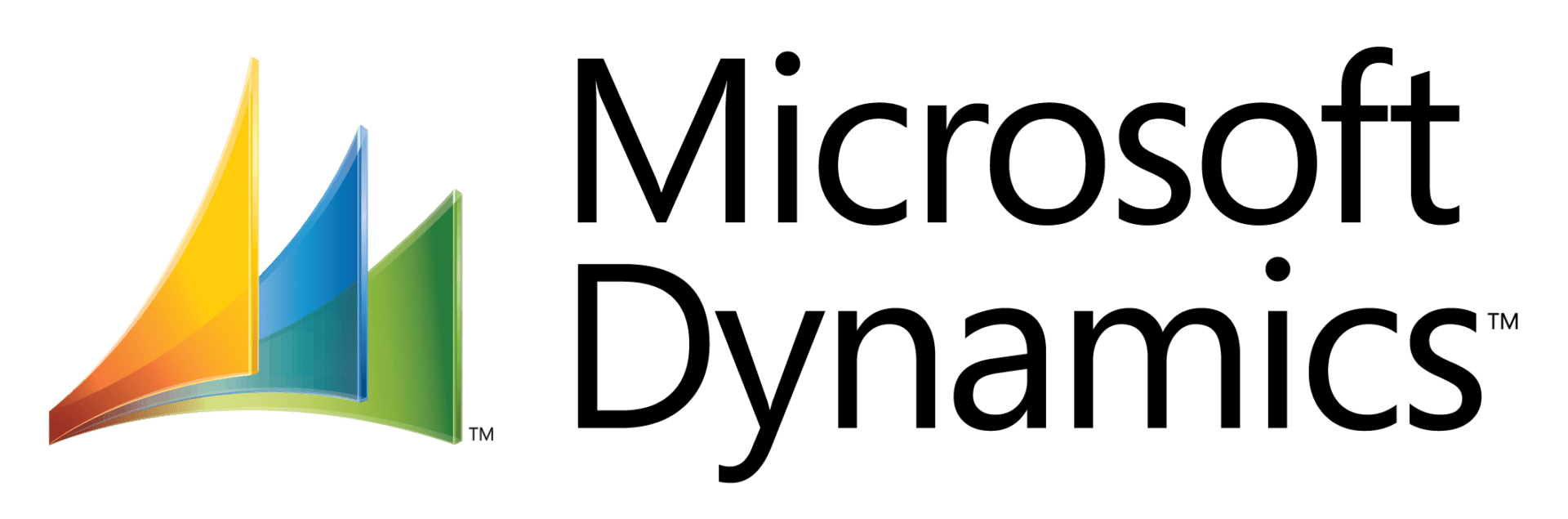
Meer implementaties of ervaringen met PROPOS?
Bekijk ook onze referentiecases! Hierin lees je alles over de keuze van Packo Inox voor PROPOS en de resultaten die het bedrijf in korte tijd heeft weten te behalen.
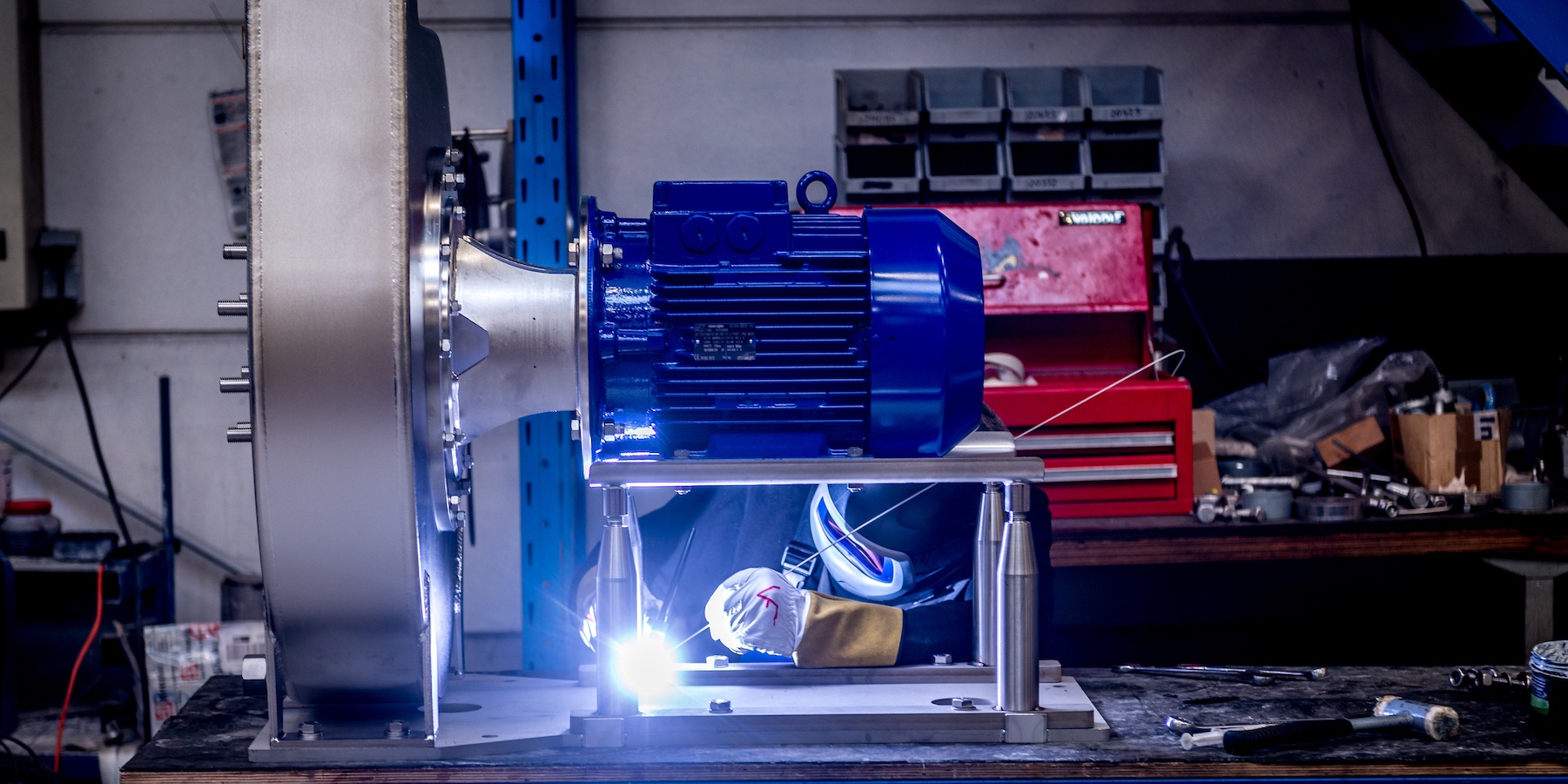
LEES MEER
Meer Belgische metaalindustrie?
Wij spraken met Jan Pauwels, managing director van PMC, een begrip in de metaalindustrie in West-Vlaanderen, over zijn drive uit te groeien tot een Factory of the Future, met behulp van PROPOS shop floor control. Het resultaat was een inspirerende case én openhartig interview over zijn weg ‘Van Crisis tot QRM‘.
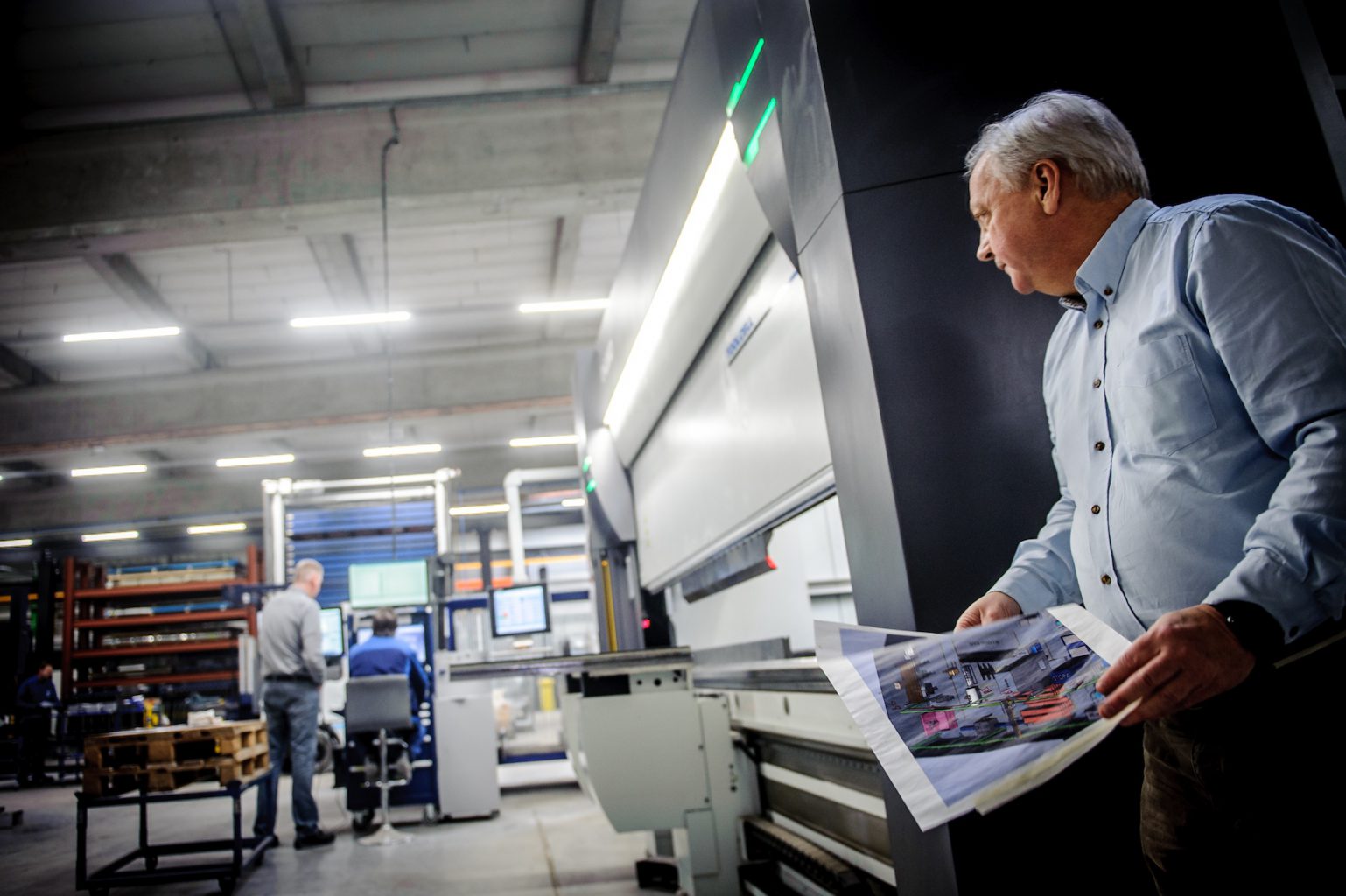
Meer weten over de voordelen van PROPOS?
Zoals bijvoorbeeld… Zelfstandig werkende medewerkers
De gebruiksvriendelijke touchscreens van PROPOS zorgen ervoor dat uw productiemedewerkers minder vragen hebben voor de productieleider. Het scherm laat duidelijk zien welke order nu prioriteit heeft, welke orders er straks aankomen en welke orders er klaarliggen in de buffer om te starten. Uw medewerkers hebben zelfs inzicht in de verwachtte drukte.
Laatste nieuws
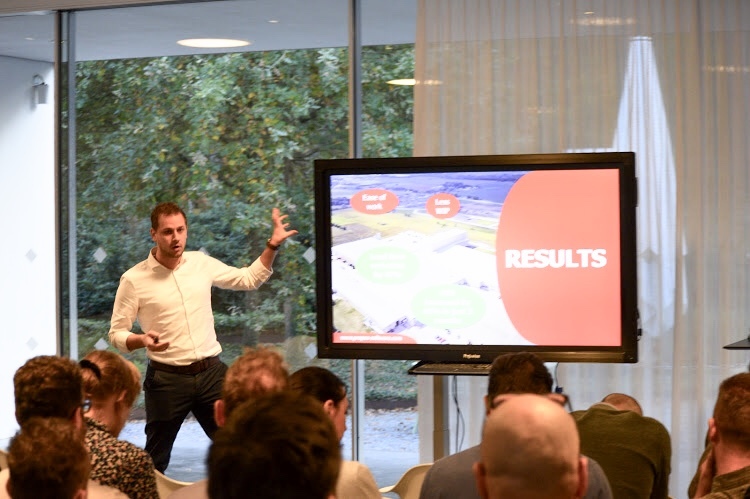
- Customer case study Merrem Kunststoffen
- Remote insight and grip on production: PROPOS at Merrem Plastics in Estonia!
- ‘Too much work in progress (WIP) is causing exploding lead times’
- Customer case System Flex: shop floor control and automation of processes
- Customer case OTM-Zenith: shop floor control for the printing industry