‘Too much work in progress (WIP) is causing exploding lead times’
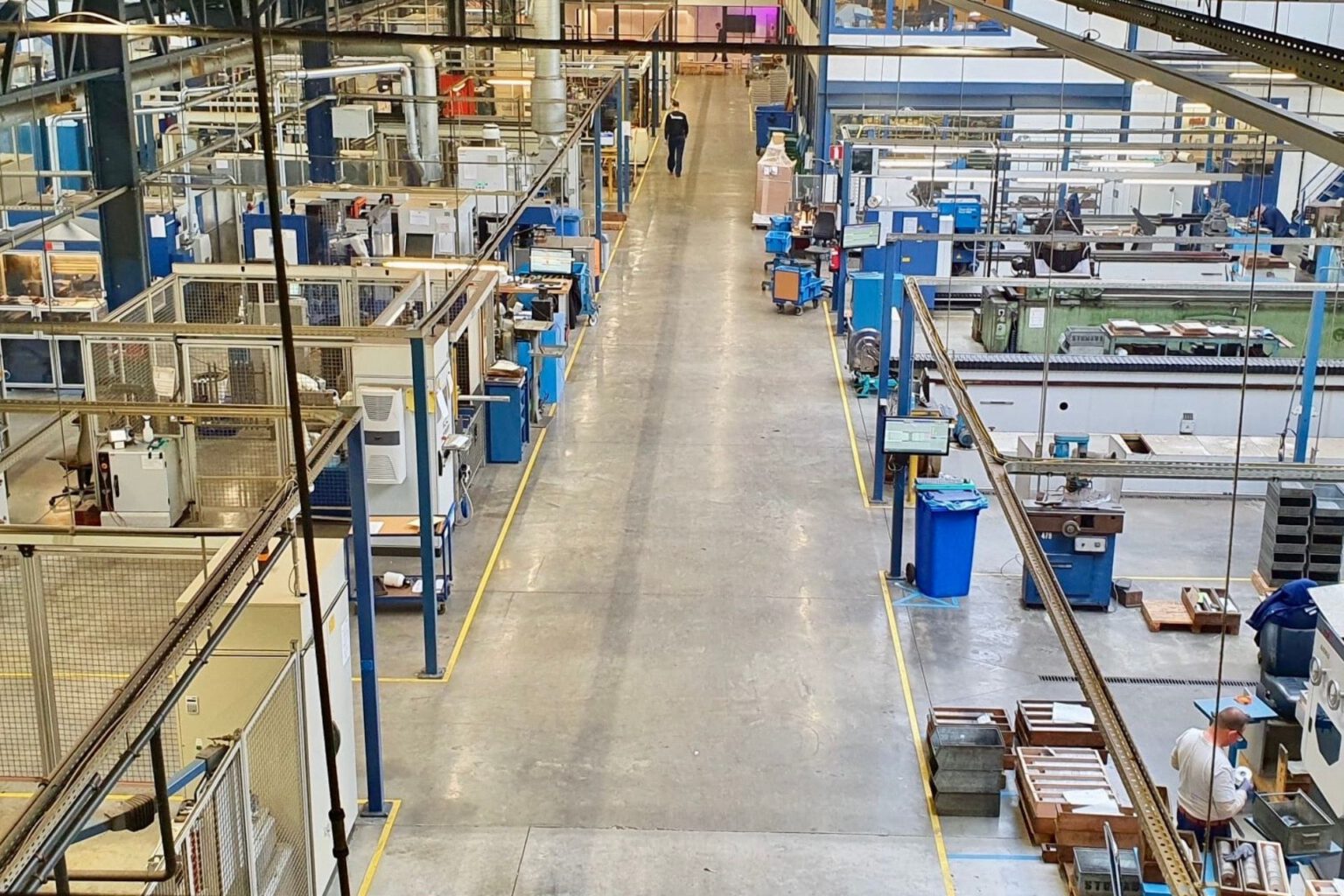
A shop floor full of orders and machines that are scheduled at a maximum capacity; it seems an ideal image for a shop floor to be busy and to get the most out of your machines. In practice, however, this leads to unnoticed negative consequences. Long lead times, employees searching for missing parts and work that stands still for an unnecessarily long time. And that results in customers having to wait too long for their orders. Quick wins can be found in tackling work in progress. In fact, less work-in-progress means better workflow and shorter lead times.